How piezoresistant sensors detect and monitor damage
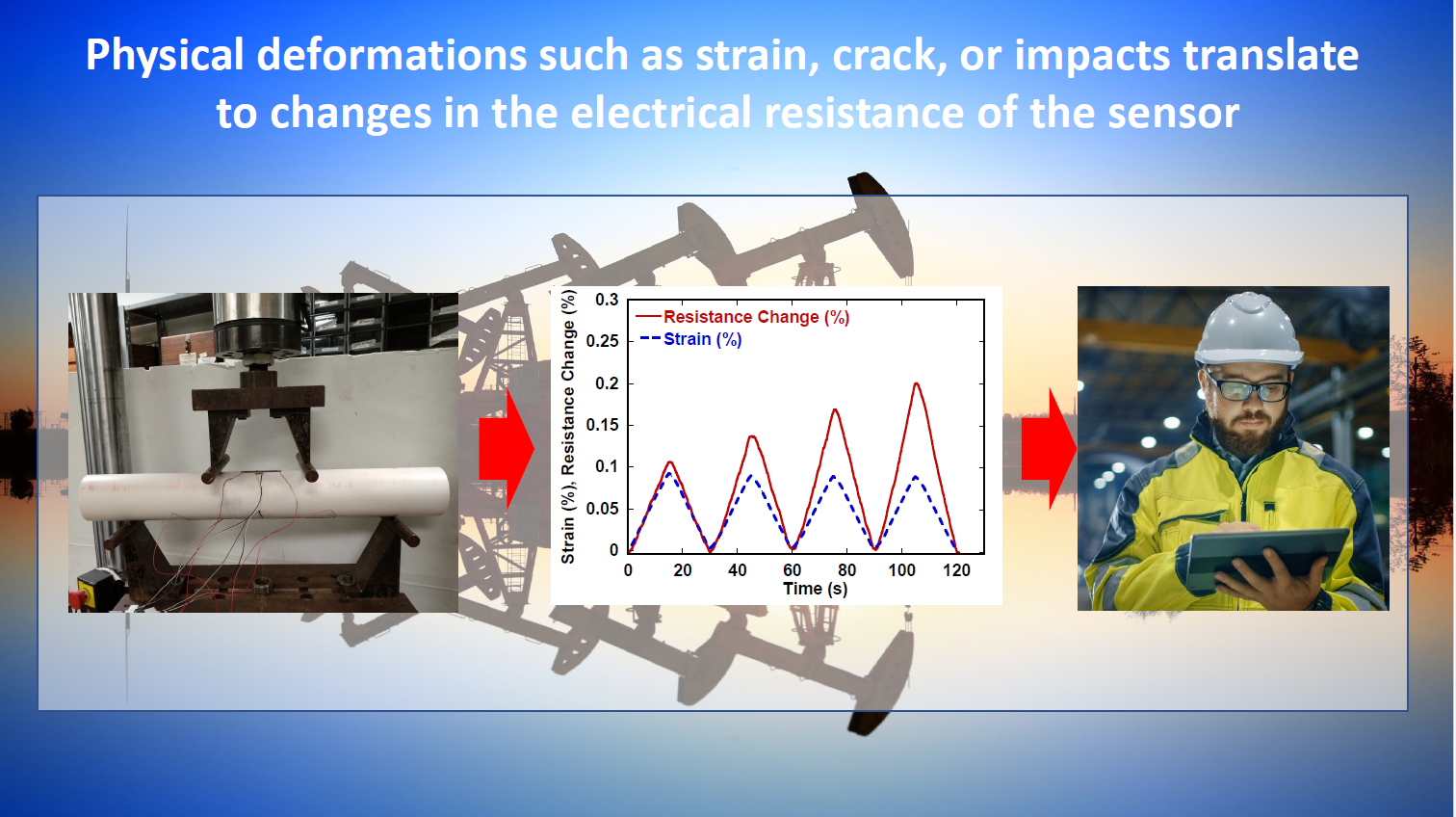
Globally, at least 6.2 million miles of pipeline transport gas, oil, and chemicals to 700 refineries, 24,500 power utility plants, and tens of thousands of industrial facilities globally, of which 60% of those pipelines are in the US. Pipeline infrastructure failures represent significant hazards in terms of personal injury (2,000-4,000 injuries/yr in the US O&G industry), environmental damage, and monetary losses due to fines, cleanups, and system shutdowns that can approach $1M/day.
MCET Technologies is developing a novel technology that can continuously monitor critical components in critical components. The technology can be applied to a variety of surfaces, including steel, wrought iron, plastic, PTFE, or composites. Because the sensors are applied as a distributive network, the sensors can monitor a wide area as opposed to limited ranges. The piezoresistant sensors can also sense strain or damage in any direction. Finally, as the sensors themselves are directly applied to the surface of the component, they sense damage, corrosion, or strain directly, and the sensing skins are flexible enough to be directly applied to diameters as small as 1”.
The small size of these sensors, combined with their ability to create electrically conductive networks offers the potential to detect deformation and damage of composite materials in situ and in real time. For example, damage in fiber composite materials can be monitored by dispersing carbon nanotubes in them. CNT-based sensors have also been used for monitoring interfacial integrity between substrate and adherents.