MCET Sensor Advantage: Sensing in Any Direction
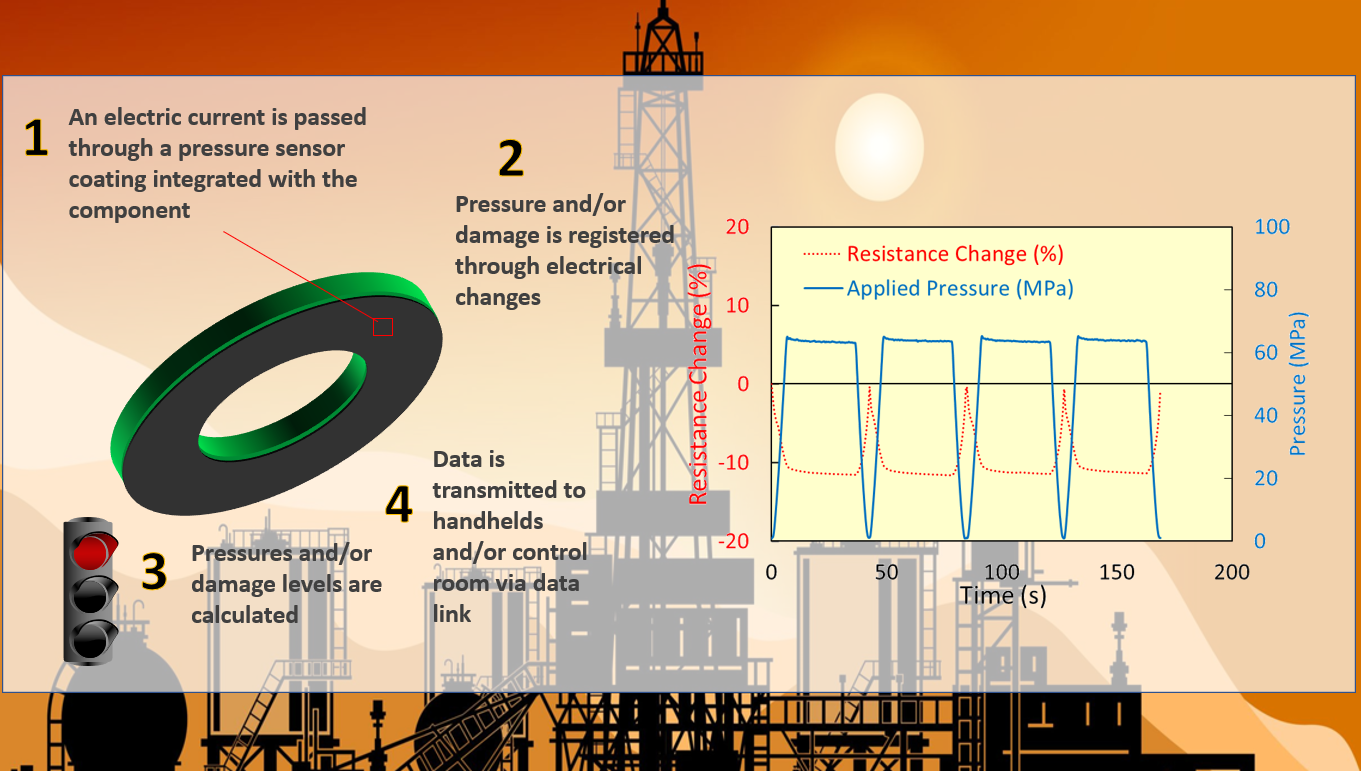
Metal structural components of pipelines, pressure vessels, and infrastructure deteriorate over their service life due to static and cyclic loading, exposure to corrosive chemicals, and harsh environments. Consequently, chemical corrosion can also result in deterioration and reduction in load carrying capacity. The result is progressive weakening of the structural elements due to section loss and cracking, and eventual structural failure if the damage is not detected in time.
While visual inspections are specifically undertaken to detect this hazard, these inspections are often only undertaken once every several years, are labor-intensive, and can only be conducted if the component is completely pulled out of service. Technology alternatives, such as fiber optics, also have limitations as they have a very limited sensing range.
MCET technologies can address these risks. As they typical carbon nanotube only has a diameter of 100nm, the application of a thin film of millions of CNTs to a surface- which can be metal, concrete, or composite (surface or fibers)- can act as a regional sensing device composed of millions of "nanoscale wires" over a surface. Moreover, the network or "skin" is piezoresistant, which means that resistance is directly related to pressure or strain applied- and can be measured on a continuous basis. This means that our CNT sensors can be extremely sensitive to pressure differentials and crack re-initiation.