CNT Monitoring & Repair- Infrastructure
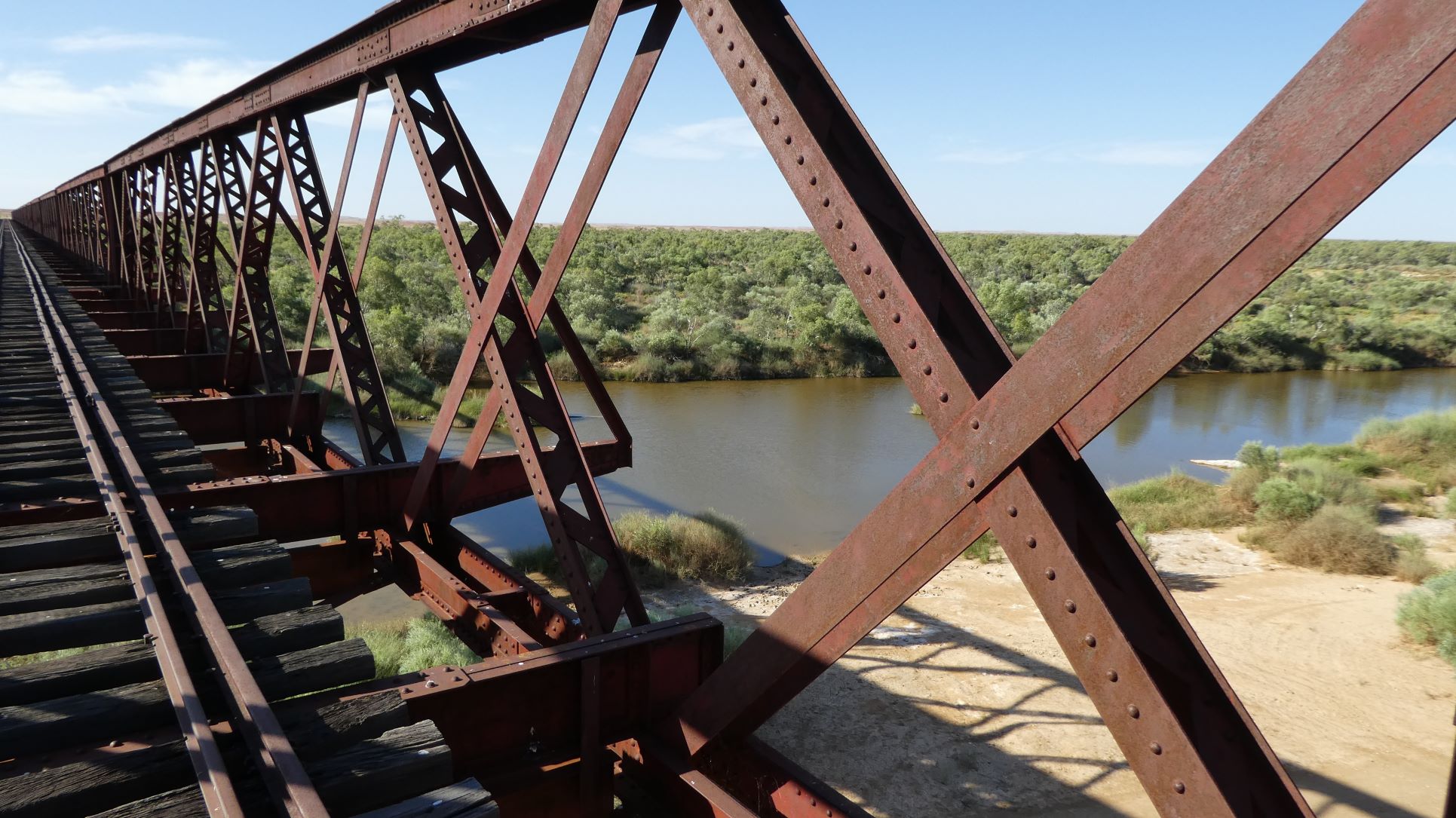
Metal structural components of aircraft, machines, vehicles, and infrastructure deteriorate over their service life due to static and cyclic loading, exposure to corrosive chemicals, and harsh environments. For example, steel bridges are particularly susceptible to fatigue cracking as increased traffic demands often exceed their design load capabilities and members often have fatigue-sensitive details. Corrosion due to deicing chemicals can also result in deterioration and reduction in load-carrying capacity. The result is progressive weakening of the structural elements due to section loss and cracking.
A series of tests were designed to evaluate our concept of utilizing the integrated CNT sensing layer to monitor crack growth underneath a composite repair. The CNT-based sensing layers can sense strain and damage and may identify the different damage, such as crack growth and debonding, by measuring conductance of its resistive network.
Tests examining fatigue crack propagation in structural steel with a composite repair and integrated bondline sensing using MCET piezoresistant sensors increased the fatigue life by 380% to over 500%, depending on configuration. The sensing layer was able to monitor deformation and crack propagation in real-time and shows potential for use in periodic inspection-based monitoring of cracks using electrical property changes.
Full paper: "Integration of carbon nanotube sensing skins and carbon fiber composites for monitoring and structural repair of fatigue cracked metal structures" Elsevier (2018)