Pipeline damage detectable through continuous piezoresistive sensors
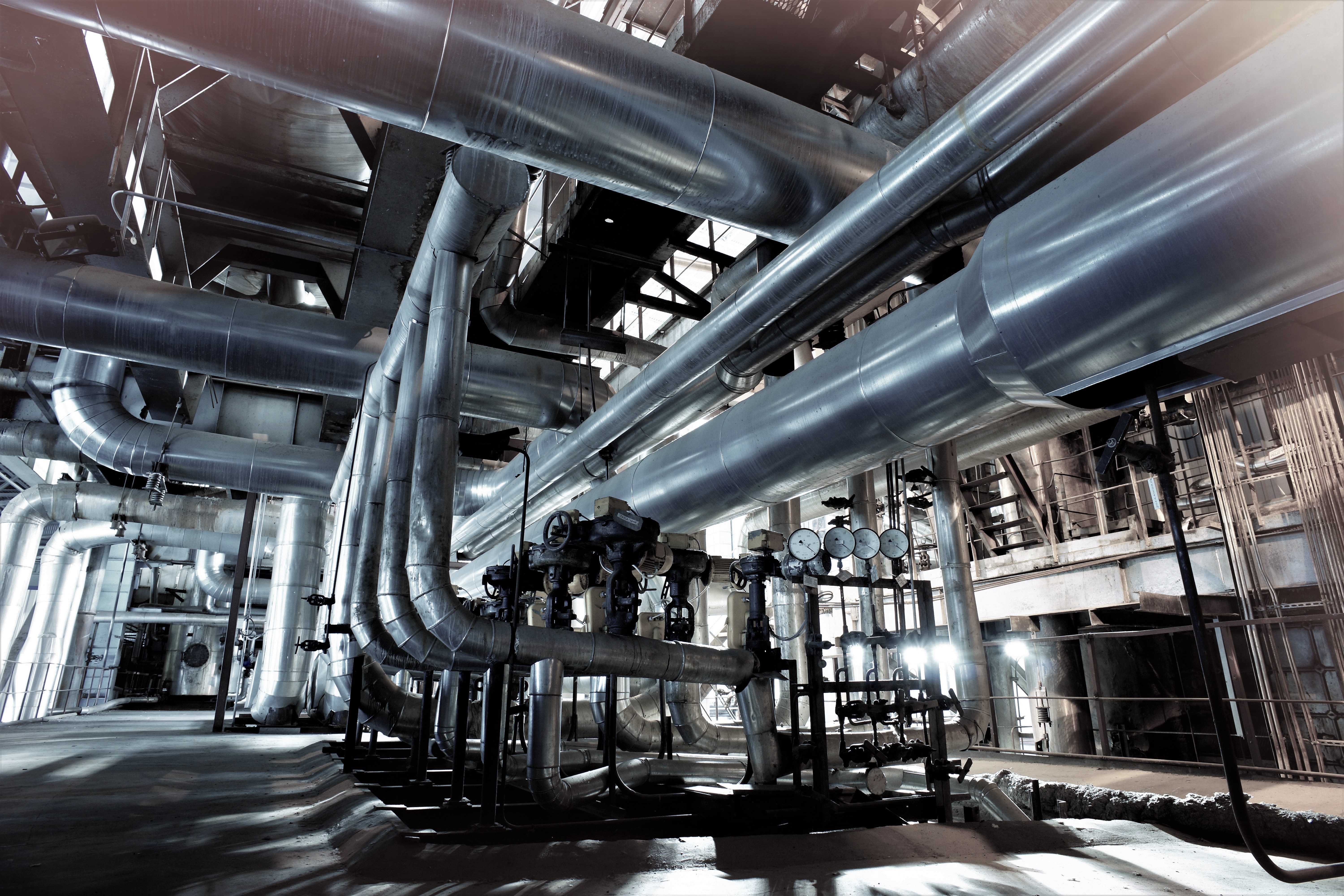
The average yearly costs of US pipeline incidents increased to approximately $733M/yr from the period of 2016-20, an increase over the previous five years. These hazards represent significant costs in terms of personal injury (2,000-4,000 injuries/yr in the US Oil & Gas industry), environmental damage, and monetary losses due to fines, cleanups, and system shutdowns that can approach $1M/day.
MCET Technologies is developing a novel technology that can continuously monitor critical components in pipelines and pipeline joints. The nano-technology is a significant advance beyond current techniques, which can rely on a periodic inspection that may happen within a period of months or even years. In other words, our technology has structural monitoring capabilities that presently do not exist in Oil & Gas and Chemical markets. The piezoresistive technology can be applied to a variety of surfaces, including steel, wrought iron, plastic, PTFE, or composites. the technology is applied as a distributive network, and the sensors can monitor a wide area as opposed to limited ranges. The nanotube sensors can also sense strain or damage in any direction. Finally, as the sensors themselves are directly applied to the surface of the component, they sense damage, corrosion or strain directly, and the sensing skins are flexible enough to be directly applied to diameters as small as 1 inch.
MCET sensors are based on a nerve-like network of electrically conductive carbon nanotubes directly applied to the component. This direct application allows for tremendous flexibility in different applications by allowing the sensor to conform to a variety of complex surfaces while the carbon nanotubes impart piezoresistive sensing capability. The sensor uses multi-walled carbon nanotubes with a resin directly applied to the material with a thickness of less than 1mm, resulting in a low-cost sensor capable of covering a large area. This “sensing skin” can be manufactured on a large-scale, enabling the distributed sensing approach. Because our sensing skin is very thin, it can used in many applications to detect the propagation of underlying cracks, structural damage, and strain on a continuous basis.