Use of NDE in non-metallic pipelines
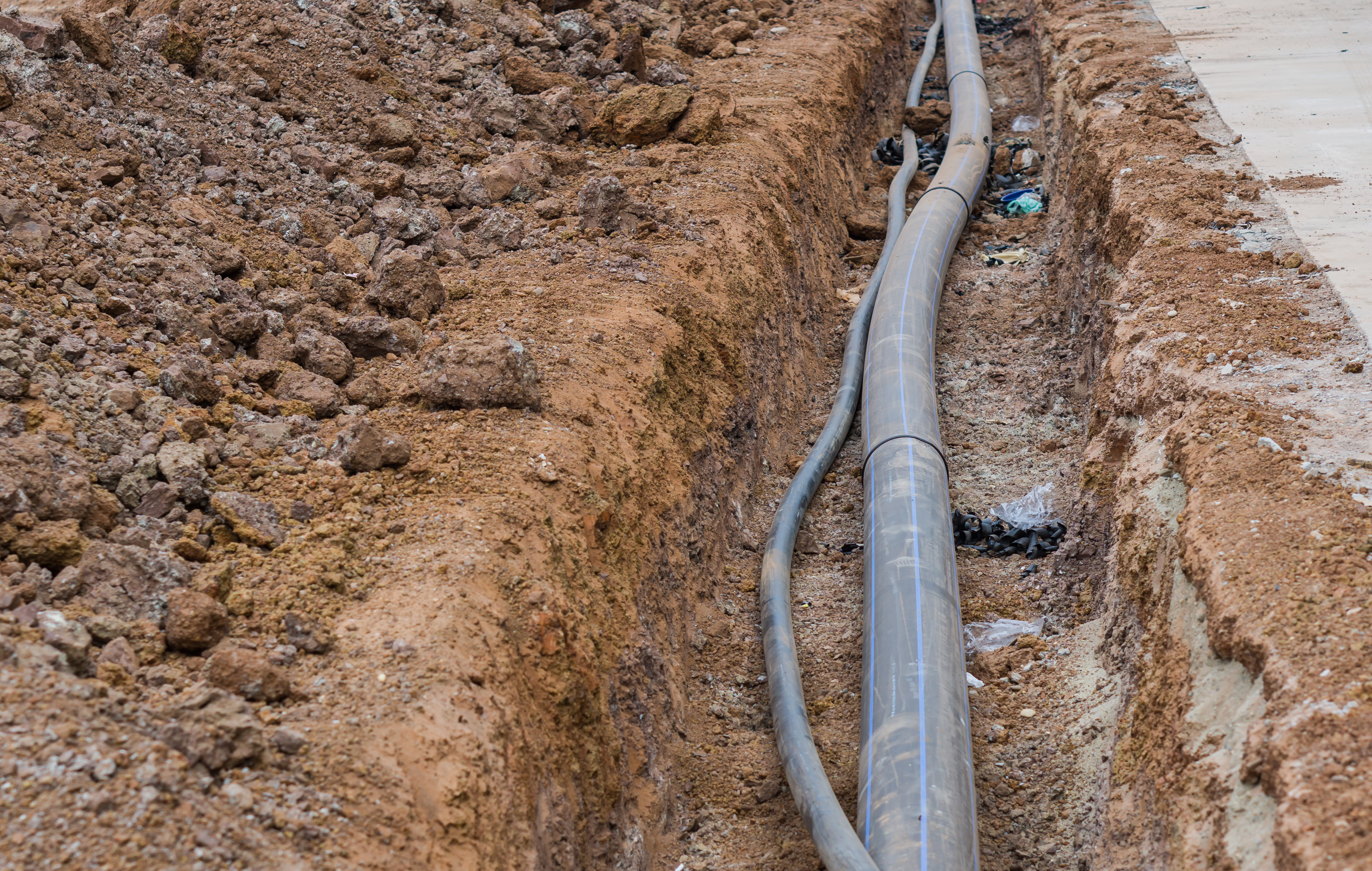
The use of non‐metallic composite pipes is increasing due to light weight and anti‐corrosion/durability related advantages. However, NDE testing methods for non-metallics can be limited, and like metallic structures, most NDE monitoring methods involve physical inspections- which can be labor-intensive and dangerous. Specific failure modes in non-metallic pipelines to be monitored in these applications are as follows:
- Hole or crack in liner due to manufacturing defect.
- Collapse or ovalization due to point loading or exceeding the minimum bend radius
- Reinforcement abrasion as a result of mishandling during installation or maintenance.
- Over tension/compression due to excessive loading during installation or abuse/negligence.
The MCET solution is to use a patented, scalable and water-based processing technique for developing flexible carbon nanotube-based sensing skins. Now, these skins are conformable and have been shown to have the capability to be wrapped around cylindrical structures as small as 1-2” in diameter, and can be used in pipes in series. The sensors can provide real-time, dynamic monitoring and feedback that can detect strain, pressure, cracks, and even impact events. The ability of applying the MCET CNT sensor network directly to a surface without FOD also has the potential to be utilized between specified layers in composite pipelines.
This capability in distributed sensing substantially increases the likelihood of detecting the initiation and propagation of localized damage that can lead to catastrophic failure. Our SHM smart skin approach can result in enhanced safety and reliability of these critical structures in Oil & Gas applications ranging from upstream to downstream applications.