MCET Completes Independent Pipe Stress/Strain Test
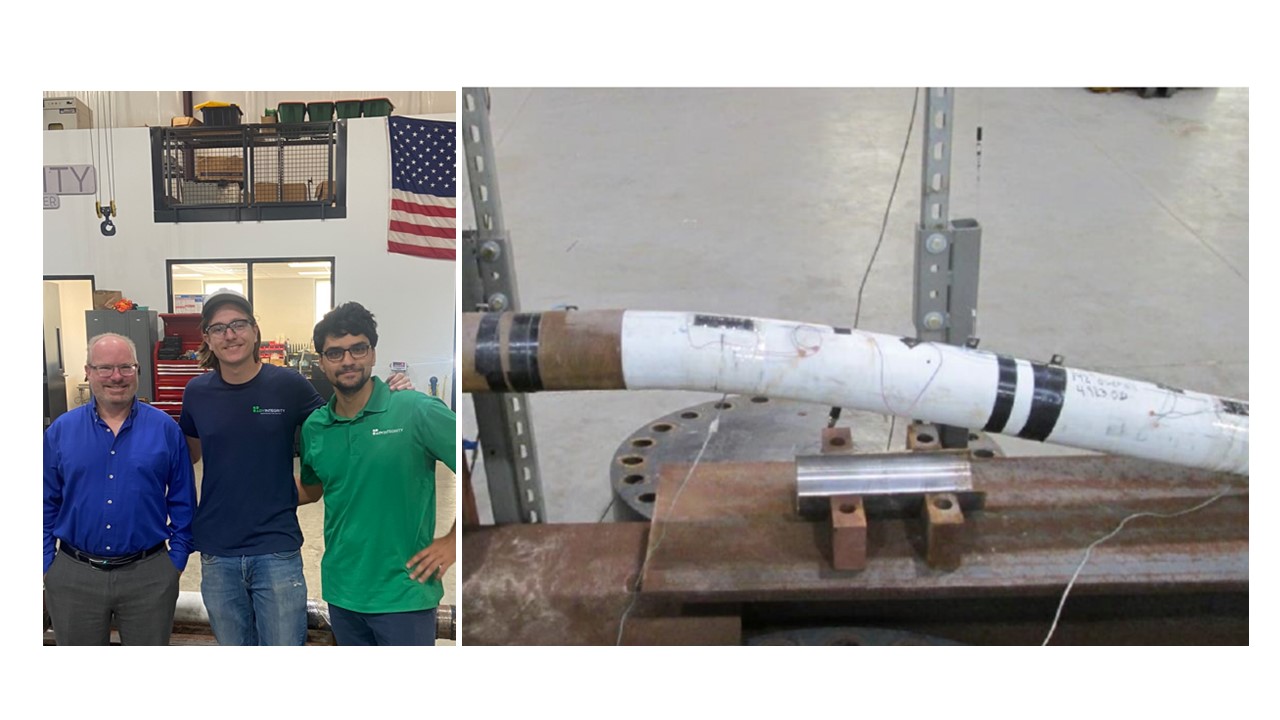
MCET recently participated in the second Combined Loading Assessment of Spoolable Pipe Systems (CLASPS-02) Joint Industry Program (JIP), a program designed to evaluate current non-destructive examination (NDE) technologies and assessment of defects caused common threats to pipelines.
What is the CLASPS-02 JIP?
The CLASPS-02 JIP was designed to address and improve the body of knowledge for the inspection and assessment gaps. This was accomplished by recreating representative threats commonly observed in spoolable composite pipelines for use as calibration baselines for NDE technologies, and to characterize the effects these threats have on the short and long-term pressure integrity. A secondary goal motivated by the PHSMA research award was to provide guidance to PHMSA on the requirements to incorporate into 49 CFR Parts 192 and 195 for spoolable composite pipes. Individual tasks in addressing these two goals included:
- Recreate common construction, ongoing operations, and 3rd party damage features on pipes with two types of reinforcements (unbonded glass tapes and aramid fiber).
- Inspected the features using currently available NDE technologies. Provided truth data to inspection vendors to calibrate and catalog NDE results.
- Conducted full-scale testing and dissection of recreated features to characterize the effects the threats have on pressure integrity and liner collapse.
- Hold an industry forum/workshop through the Composite Technology Users Group (CTAG)1 to communicate results of the inspection work (Q1 or Q2 of 2024).
- Include recommendations on design, operation, maintenance, and integrity management aspects for Part 192 and 195 based off industry standards.
What were the tests performed on MCET Technology?
Several tests were performed on the MCET CNT sensors, including:
-
Threats 6&7: excess tension- excess tension simulations were performed to the sample tension load. MCET sensors were placed at the center and quarter points of the sample (halfway between the middle and endcap). The high-level test procedure included the following load steps:
- Pressurized sample to 100 psig and maintained.
- Applied axial load at a rate of 0.1 inch/min until the axial load rating was achieved.
- Held load for five minutes to allow for acoustic emissions monitoring.
- Slowly released load from the sample.
- Pressurized sample up to NPR (1,500 psig).
- Applied axial load at a rate of 0.1 in/min until sample failure or gross plastic deformation was observed (increase in displacement with no increase in load).
-
Threat 10- localized bending (at fitting end)- using a test fixture, the end fitting of a sample was raised inducing an "S" bend. A curved "stinger" prevented kinking at the fixture point, 72" from the end fitting (between the test frame and sample). The end fitting of the pipe was raised to 2.5" and held for 1 minute before continuing to 6". The sample was held for approximately 4 minutes at 6" of displacement before being unloaded to a relaxed position.
How did the MCET sensors perform?
The carbon nanotube strain sensor tests demonstrated that this is a promising technology that is in the early stages of development. The resistance of the nanotube sensor correlated well with adjacent strain readings considering both tension and bending loading. While the sensors are still in early stages of development, and did experience bonding/adherence issues at high levels of strain, it was determined that the CNT technology is promising and worthy of further work and refinement.
Conclusion/next steps
Structural health monitoring (SHM) is an essential tool for ensuring the structural integrity and safety of pressure vessels. By detecting early signs of damage and predicting potential failure, SHM can help optimize maintenance activities, reduce costs, and extend the service life of pressure vessels. Although there are several challenges associated with its application, SHM remains a valuable technique for ensuring the safe and reliable operation of pressure vessels in a wide range of industries.
MCET will participate in more tests that show detection rates both in sensors placed on the surface of composite pipes and as "embedded" sensors in both composite pipes and composite pipe repairs.