What is SHM in Pressure Vessels?
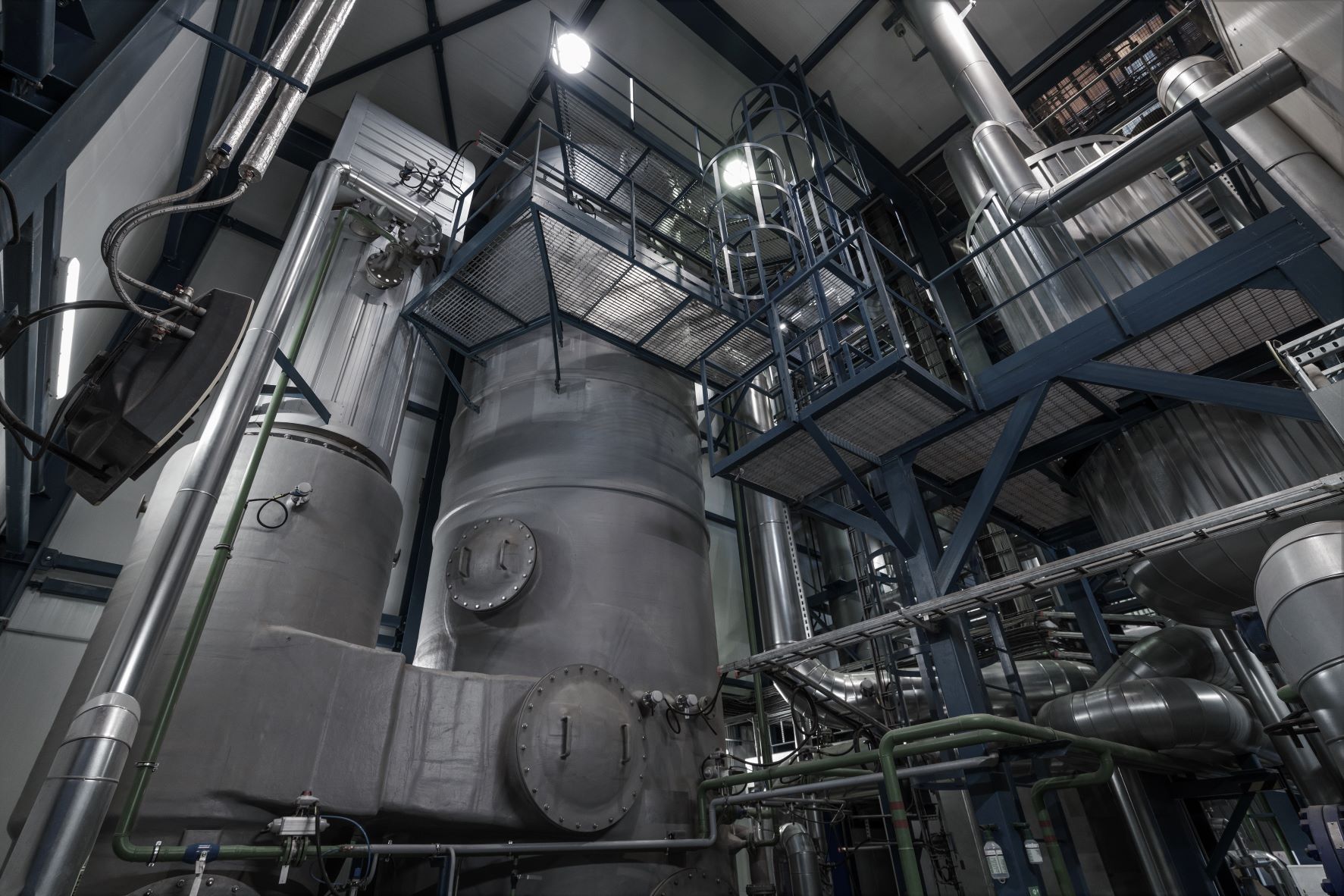
Pressure vessels are crucial components in a wide range of industries, including oil and gas, chemical processing, and power generation. These vessels are designed to store, transport, or process pressurized fluids, gases, or other substances. As pressure vessels are subject to high stress and fatigue loads, they require regular inspection and monitoring to ensure their structural integrity and prevent catastrophic failure. In this blog, we will discuss structural health monitoring (SHM) in pressure vessels, including its benefits, techniques, and challenges.
What is Structural Health Monitoring (SHM)?
Structural Health Monitoring (SHM) is a process of continuous or periodic monitoring of the physical condition and behavior of a structure to detect any signs of damage, deformation, or degradation. The SHM process involves installing various sensors, such as strain gauges, accelerometers, acoustic emission sensors, or ultrasonic sensors, to measure the structural response to external loads or environmental conditions. The data collected from these sensors are then analyzed using advanced algorithms and models to assess the structural health and predict potential failure.
Benefits of SHM in Pressure Vessels
The application of SHM in pressure vessels offers several benefits, including:
-
Early Detection of Damage: SHM sensors can detect the early signs of damage, such as cracks, corrosion, or deformation, before they become critical and cause catastrophic failure.
-
Reduced Maintenance Costs: SHM can help optimize maintenance activities by identifying areas that require repair or replacement, minimizing downtime and maintenance costs.
-
Increased Safety: By continuously monitoring the structural health of pressure vessels, SHM can improve safety and prevent accidents or injuries.
-
Extended Service Life: SHM can help extend the service life of pressure vessels by detecting and mitigating the effects of fatigue, corrosion, and other degradation mechanisms.
Techniques for SHM in Pressure Vessels
There are several techniques used for SHM in pressure vessels, including:
-
Strain-based Monitoring: Strain gauges are used to measure the deformation of the pressure vessel caused by internal or external pressure. The data collected from these sensors can be used to calculate stress levels and detect any changes in the structural behavior.
-
Acoustic Emission Monitoring: Acoustic emission sensors can detect the high-frequency noise generated by crack propagation or other damage mechanisms. This technique can provide information about the location, size, and severity of the damage.
- Carbon Nanotube Sensing: Carbon nanotubes (CNTs) have the potential to revolutionize the way we detect and measure various physical and chemical parameters, including temperature, pressure, strain, and damage.
-
Ultrasonic Testing: Ultrasonic sensors can be used to measure the thickness of the vessel wall and detect any defects or corrosion. This technique is commonly used in the inspection of welds, flanges, and other critical areas.
Challenges of SHM in Pressure Vessels
Despite the benefits of SHM, there are several challenges associated with its application in pressure vessels, including:
-
Sensor Placement: The accurate placement of sensors is critical for effective SHM. In pressure vessels, access to some areas may be limited, making it challenging to install sensors in the optimal location.
-
Data Analysis: The analysis of SHM data requires advanced algorithms and models that can accurately interpret the sensor signals and provide meaningful information about the structural health.
- Composite Materials: Composite pressure vessels (COPVs) have a unique set of challenges in that many established methods of SHM are either ineffective or unreliable. Also, failures occur due to debonding- which is difficult to detect.
-
Integration with Maintenance Programs: SHM should be integrated with the maintenance programs to ensure that the detected damage is appropriately addressed, and the required repairs or replacements are performed.
Conclusion
Structural health monitoring (SHM) is an essential tool for ensuring the structural integrity and safety of pressure vessels. By detecting early signs of damage and predicting potential failure, SHM can help optimize maintenance activities, reduce costs, and extend the service life of pressure vessels. Although there are several challenges associated with its application, SHM remains a valuable technique for ensuring the safe and reliable operation of pressure vessels in a wide range of industries.